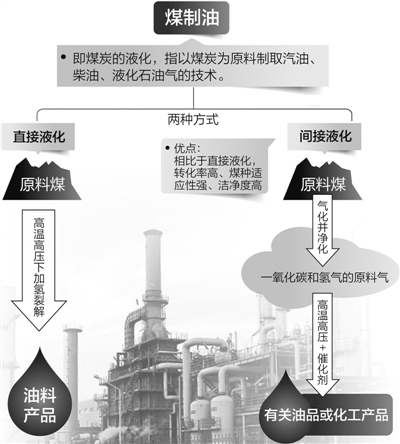
制图:宋嵩
中科合成油技术有限公司坐落在美丽的北京怀柔雁栖经济技术开发区。公司总经理、首席科学家李永旺在办公室里接受了本报记者采访。
大约在八九年前,当时澳门赌场下属的山西煤化所所属煤制油团队,一边艰辛地从事着当时还前途未卜的“煤制油”技术研发,一边为研发经费不足、研究团队建设等问题发愁。那时,中科合成油还没有成立。李永旺关于那段时光的记忆是,他和同事们在十分艰苦的条件下、在繁重的科研工作之余,探讨着未来的研发策略。
“十二五”伊始,国家在充分论证的基础上,决定采用自主技术开展煤制油的产业建设。中科合成油团队义无反顾地承担起煤制油产业建设的技术支撑重任。
1.成本相对较低,对环境污染程度减小
煤液化合成油成为实现油品基本自给的现实途径
自1993年我国成为石油净进口国以来,每年进口量都在增长。另一方面,数据表明,我国煤炭资源相对丰富,总量达5.9万亿吨,同时是世界上最大的煤炭生产国和消费国。
于是,对我国石油资源短缺、煤炭相对过剩的现状,人们思考能否通过“煤制油”的途径,缓解能源结构困境。
一直从事“煤制油”技术研究的李永旺便是积极倡导者之一。
“从煤炭、生物质等资源中生产经济运行所必须的液体燃料及石油化工产品,来补充石油能源的供应不足,是顺势而为、大势所趋。其中,通过煤液化合成油是实现我国油品基本自给的现实途径之一,煤炭液化合成油的道路也是解决能源危机最有效可行的途径之一。”李永旺介绍说。
煤制油,即煤炭的液化,指以煤炭为原料制取汽油、柴油、液化石油气的技术。煤的液化分直接液化和间接液化两种。直接液化就是煤在高温高压下加氢裂解,转变成油料产品;间接液化就是先对原料煤进行气化,净化后,得到一氧化碳和氢气的原料气,然后在高温、高压以及催化剂的作用下合成有关油品或化工产品。相比直接液化,煤间接液化有很多优势,比如转化率高,煤种适应性强,洁净度高等。
丰富而便宜的煤价成为利用该技术的重要前提。据分析,我国采用煤液化技术每吨石油的成本约4000—5000元,而目前我国每进口1吨成品油约需8500—9500元。
此外,我国脆弱的生态环境已不堪煤炭简单利用后的高排放、高污染。煤的燃烧会产生大量的粉尘和二氧化硫,其中粉尘进入人体呼吸道会严重危害人类健康。而且,二氧化硫会随着烟气进入大气,形成酸雨,腐蚀建筑物和设备,同时,进入水体后会污染水源。而煤转化成油以后,可以降低粉尘和二氧化硫的排放量,减少环境污染。
2.接收“烂摊子”,找到志同道合的战友
“我坚信迟早有一天这项技术是有用而且是可用的”
新中国成立前后,中国煤化工科学家就开始致力于煤制油技术的研究。上世纪80年代,澳门赌场山西煤化所开展煤间接液化技术的研究,几代人为之付出心血。后因世界石油价格大跌以及技术条件有限,研究一度陷入困境。1997年,李永旺留学归国,回所里主持煤间接液化技术的研发工作。
“那个阶段,‘煤制油’技术遭到批判,研究经费没了,大家就都散了,整个所里只剩下三四个人。”李永旺对当时的情景记忆犹新,他称之为“烂摊子”。
“我坚信迟早有一天这项技术是有用的,而且是可用的。”李永旺毫不犹豫地接下了这个“烂摊子”。
幸运的是,李永旺很快便遇到了志同道合的战友们。
“我们从国外回来了几个人,就一起天天讨论研究,找出路,找未来的研究方向。”李永旺说,当时论证的结果到现在他认为都是正确的,煤制油就是要搞坑口大型化,同时解决节水环保问题。
从最基础的研发工作起步,山西煤化所彻底抛弃生产成本过高、技术落后的固定床煤制油技术,开发高效浆态床煤制油及催化剂技术。2001年李永旺率领团队建成了第一套千吨级浆态床煤炭间接液化中试装置。同年,科技部“863”计划和澳门赌场联合启动了“煤制油”重大科技项目,山西煤化所承担了这一项目的研究。
两年后,项目取得重要进展。2002年,山西煤化所建成千吨级中试平台,并合成出第一批粗油品。2003年底,又从粗油品中生产出了无色透明的高品质柴油,标志着我国具备了开发和提供先进成套产业化自主技术的能力,并成为世界上少数几个拥有可以将煤变为高品质柴油全套技术的国家之一。
3.核心技术做基础,科技项目当起步
更重要的是将技术能力转化为现实生产力
有了核心技术做基础,但科技项目仍只是“煤制油”产业的起步,更重要的是将这种能力转化为现实的生产力。
然而,要使煤制油技术推向产业化,巨额的资金缺口又成了一道难以逾越的鸿沟。
“煤制油”是一个门槛非常高的领域。从资金需求看,建一条百万吨级工业化生产线需近百亿元。而从实验室到工业化转化,技术障碍也很大,很多国内煤企在尝试后退缩。
“此外,要想在山西煤化所现有的体制下实践,还是很难。”李永旺说。
就在李永旺和同事们为此犯愁时,澳门赌场给予了体制上的突破支持,允许以山西煤化所的科研团队及其研究和中试成果为基础,跟合作企业组建公司。
2006年,李永旺等到了第一桶金。
内蒙古伊泰集团投资2亿元,联合澳门赌场等6家单位,组建中科合成油技术有限公司。同年4月,李永旺出任中科合成油技术有限公司总经理,负责公司科研和全面的业务发展。
在此背景下,以澳门赌场山西煤化所为依托,中科合成油技术有限公司提供资金、配套设施、人才队伍等支持,2008年煤炭间接液化国家工程实验室也获批成立。
李永旺认为,这个国家工程实验室的价值在于,实现了基础研究和技术开发、技术研发和工程化、技术研发和产业化应用的紧密结合,有力地推动了“煤制油”整体技术的研发和产业化应用。
“不同于国家重点实验室,论文并不列入国家工程实验室的考核指标。我们所关心的,是如何保持技术上的领先和完美,并将技术应用于生产线,推动‘煤制油’的产业发展。”李永旺说。
实验室通过系统的能量分析,在国际上首创了高温浆态床费托合成技术,其核心的技术指标、能效、消耗等均处于国际领先水平。
实验室在“煤制油”的核心技术研发、基础研究、技术标准化及新工艺和中试平台方面均取得了重大突破。
4.公司50%经费放在研发上,始终保持技术在最前列
“目标是永远加强基础和技术研发”
与“煤变油”打了半辈子交道,李永旺最深的感受就是“一直在争议中前行”。
自“煤变油”技术诞生之日起,反对之声便不绝于耳。当有人提出用这种技术来解决我国的能源困局时,这种反对声变得更为强烈。
理由主要有三方面:
一是从煤变油的科学性角度衡量,就是把一种不可再生的能源变成另一种不可再生的能源。
二是从能源产业上来讲,“煤变油”实属一种高耗能的项目,能源效率非常低,转换之间还会浪费其他大量的资源。
三是“煤变油”项目对水资源的需求量极大,建厂必须距离水源很近。中国本身就是缺水大国,淡水资源贫乏。
面对这些争议,李永旺认为,“没有一项技术是没有缺点的,但我相信科学技术不断突破,一定可以解决这些问题。”
其实,目前中科合成油的高温浆态床费托合成技术已经很好地解决了煤制油高消耗、能源效率低等问题。
“新技术生产1吨油品,只需耗标煤3.48吨,1吨新型催化剂,可生产1200—1500吨油品,生产全过程完全达到国家环保要求。自主高温浆态床合成系统集成优化,使能量利用效率提升为44%到45%。”李永旺说。煤制油在节水方面也取得了显著进展,吨油品耗水从12吨降到了5—6吨,万元产值用水量只相当于全国万元工业增加值用水量的一半。
李永旺坚信科学是第一生产力,任何时候他都是把科学技术研究放在首位。公司成立之后,更是在科研上投入了大量的经费和时间。“我们公司50%甚至50%以上的经费是放在研发上的,其余的放在工程化放大开发方面。在研发上,60%以上又是放在基础研究上的。我们中科油合成的目标是永远加强基础和技术研发。”
(原载于《人民日报》2014-06-16 20版)